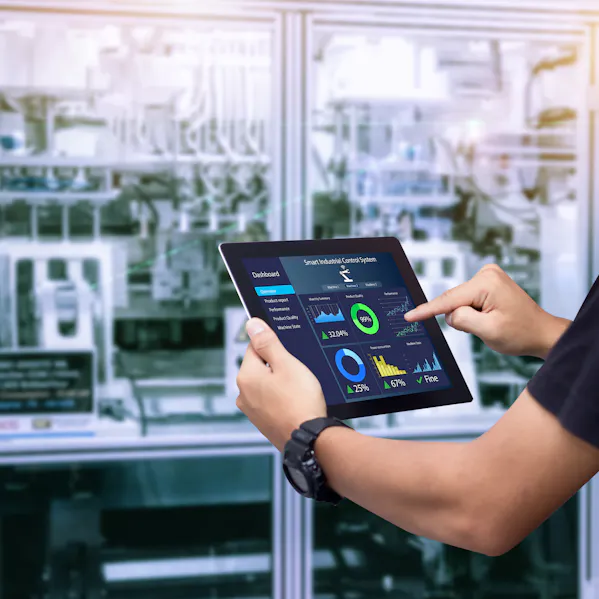
Spare parts management and digital twin
For the manufacturing industry, spare parts management is an important part of the aftersales business. Whenever machines are in operation around the clock, wear and tear and breakdowns are an unwanted but constant companion. For any maintenance or repair of a damaged machine, it is essential to identify and order spare parts quickly and correctly. To do this, the maintenance engineer needs an overall view of the affected machine, appropriate documentation, and instructions for installation and removal, possibly also as a video or 3D drawing.
Modern spare parts management uses the potential of digitalization. The self-service portal, which optimizes communication between the customer and the service provider and drastically simplifies certain processes, becomes the key element.
Definition of individual maintenance cycles
Automatic transmission of machine measurement data
Timely shipment of spare parts
Advance planning of the technician's deployment
Your benefits
Simple spare part identification
Customer loyalty & recurring revenues
Higher customer satisfaction & turnover
Accelerated ordering process of spare parts & higher transparency
Spare parts management
Our solution
Make the digital machine file for your machinery accessible to your customers in a customer and service portal. Create a central contact point for all questions.
Digital machine file in the customer & service portal includes:
Entire history of a machine
Maintenance services on demand, certifications, construction plans in 2D or 3D
Fast, efficient spare part/component identification via 2D/3D drawing
Identification of spare parts by means of AI (artificial intelligence)
Machine data acquisition via sensors
Link with integrated webshop
IoT connection
Equipment Viewer (add-on SAP Commerce Cloud)
With the All for One Customer Experience Equipment Viewer, machine and plant manufacturers offer their customers a unique tool for spare part identification: The intelligent navigation quickly leads to the component you are looking for and provides accompanying documentation. If the relevant part not in stock? No problem! The integration into the SAP Commerce Cloud allows ordering in just a few clicks.
Learn more
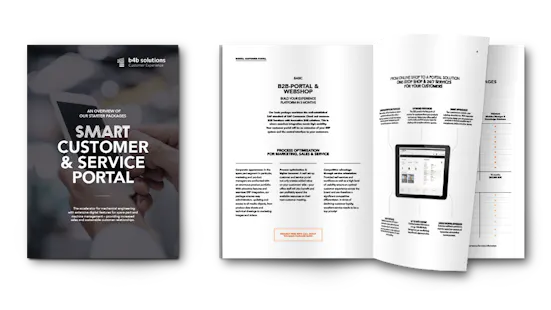
Do you have any questions?
We are happy to help you!
Your contact for Customer Experience
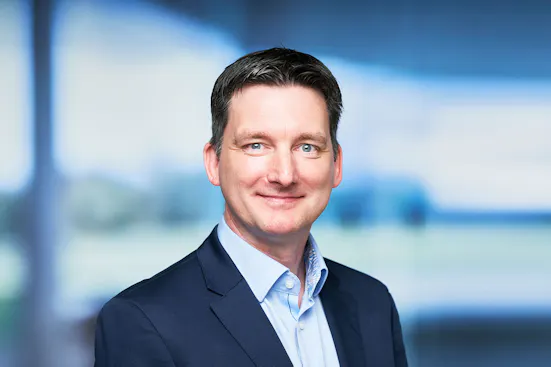